Preparation of Ores |
|
Metalliferous
ores straight from the mine are seldom directly suited for
metal smelting. Quite often their metal content is too low
e.g., only 0.8% copper or 5% lead for processing in the furnace,
or they may be composed of minerals containing different metals
requiring different kinds of metallurgical treatment.
|
|
For
these reasons, must ores have to undergo variety of preparatory
processes, referred to as dressing for the removal or separation
of waste matter or other minerals, so that the concentration
of the desired mineral is increased. Some of the processes
used more particularly in ore dressing are sorting; comminution
(crushing and grinding); sizing (by screening); classifying
(e.g., the grading of finely divided material by rates of
settling); separation (e.g., by magnetism, electrical conductivity,
specific gravity, etc.). |
|
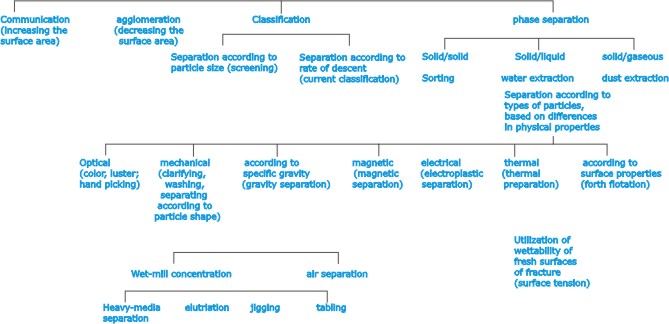 |
|
The
preparation plants are basically situated at the mines, so
that only the processed ore, free of waste matter, has to
be transported to the smelting works. Preparation starts with
crushing and grinding (Fig.1). The degree of comminution (size
reduction) to be applied will depend on the size of the ore
lumps and on the requirements of the subsequent treatment
to be applied. Sizing and classifying i.e., grading the comminuted
material according to particle size are important operations
in ore dressing. To relieve the crushing and grinding machines
of unnecessary load, particles that have been sufficiently
reduced in size are removed by screening (Fig.5).
|
|
Sizing
of relatively coarse particles can most efficiently be performed
by screening, and screens of many kinds are used for the purpose.
Small particles below about 1mm in size can usually be more
suitably sized by classification based on different rates
of settling of different particles sizes in water. For e.g.
the Hardinge countercurrent classifier (Fig.6) is slowly rotating
drum on the inner surface of which are located spiral flanges.
As the classifier rotates, the coarser particles are settled
out, moved forward by the spiral flanges, and repeatedly turned
over in a forward motion, releasing any finely divided material
mixed with them. |
|
It
is not possible, within the scope of this article, to describe
all the many processes and types of equipment employed in
the preparation of metalliferous ores. However, three important
methods of treatment will be dealt with. |
|
|
|
In
wet-mill concentration the differences in specific gravity
of different minerals are utilized for separating them. The
metalliferous ores – sulphides and oxides – are
as a rule specifically heavier than the waste material. Separation
of the ore from the waste may be effected in a settling classifier
with the aid of water in motion, the underlying principle
being that the differences in specific gravity are associated
with different rates of settlement of the particles (Figs.
2 and 7).
|
|
Coarser
particles, ranging in size from about 0.5 to 30 mm, can be
settled out in a machine known as a jig in which a horizontal
stream of water is subjected to a rhythmical up-and-down motion.
Finer-grained materials, approx. 0.3 to 0.5 mm in size may
be treated on a table concentrator a slightly inclined plate
on which the lighter material is separated from the heavier
by a thin, shallow stream of water. |
|
This
hydromechanical separating action may be augmented by the
action of gravity developed by oscillating or jolting motions
applied to the table (shaking and bumping tables Fig.4) these
concentration processes are referred to as tabling. |
|
Flotation
is an important and commonly used separation process which
is based on the fact that some of the components in the comminuted
minerals are wettable, whereas others are water-repellent
(hydrophobic Figs 3 and 8). The hydrophobic particles have
an ability to hold air bubbles by surface action, the nature
of the film on the outside of the particles being the controlling
factor. |
|
Finely
divided air which is introduced into the pulp the mixture
of solids and water in which flotation is performed, adheres
in the form of bubbles to these particles, more particularly
the metalliferous components of the pulp, and causes them
to rise to the surface. Here they collect in a mass of froth
and are removed by a skimmer device. The hydrophilic components
remain behind in the pulp. As a rule, these are the worthless
minerals (gangue), which are removed as tailings from the
flotation machine.
|
|
The
sulphides of heavy metals are readily floatable, and flotation
is therefore an important method for the concentrating of
copper, lead and zinc ores. A further development has been
the selective flotation of two or more useful minerals, particularly
the ores of different metals, which can thus be collected
as separated concentrates This principle is, for example,
applied to the preparation of sulphidic lead-zinc ores.
|
|
The
floatability of minerals can be controlled by certain chemical
additives called flotation agents. These are of various kinds:
Frothers, whose function is to produce froth by combining
the air bubbles into a stable froth which will buoy up the
ore particles. Oils and allied substances are used as frothers.
|
|
Collectors
are substances that increase the water repellency and make
the ore particularly receptive to the attachment of air bubbles.
Collectors usually consist of synthetic organic compounds.
|
|
Other
flotation agents help to regulate the process. Other depressors
can make hydrophobic minerals temporarily hydrophilic and
can in this way help in the selective separation of one mineral
from another by depressing one, thereby inhibiting its flotation.
The depressed mineral can subsequently be made hydrophobic
again by an activating agent. The various agents for regulating
the flotation process in this manner are inorganic compounds,
mostly salts. |
|
Magnetic
separation: If a comminuted and classified ore is brought
into a magnetic field, the magnetic components generally the
useful metalliferous ore can be extracted and thus separated
from the nonmagnetic residual material. The treatment is carried
out with the aid of magnetic separators, of which there are
many kinds. |
|
A
drum separator is explained in Fig.9. This method of separation
plays an important part, for example, in the concentrating of
certain iron and manganese ores. Those substances which are
attracted by a magnetic field are called paramagnetic. These
are subdivided into strongly magnetic and weakly magnetic substances.
|
|
Various
techniques have been applied for the separation of both categories
of material. In general, magnetic fields of greater intensity
high intensity magnetic separators have to be employed for
dealing with weakly magnetic ores. In both categories wet
and dry processes are employed, depending on whether or not
water is used as an aid in the process.
|
|
The
magnetic properties of certain ferrous minerals can be enhanced
by suitable preliminary heat treatment. For instance, in the
case of siderite a particular kind of iron ore, which is a
carbonate-FeCO3 the carbon dioxide can be expelled by heating
the ore in a kiln. As a result, the carbonate is converted
into the strongly magnetic compound named ferroso-ferric oxide
(Fe3O4), which can readily be separated by a magnetic action.
|
|
o
DISCLAIMER o
CONTACT US |